“Learn how pharmaceutical manufacturers can maintain quality and safety in drug manufacturing by complying with GMP standards. Key areas include sampling, testing, validation, and quality control.”
The pharmaceutical industry is one of the most important industries which allow for safe and effective medications to be available for patients across the globe. Regulatory agencies like the Food and Drug Administration (FDA) have set strict standards, including the Current Good Manufacturing Practice for Finished Pharmaceuticals to ensure all drugs are manufactured with the highest quality and safety. As part of this regulatory landscape, there are requirements for sampling and testing (i.e., biological tests); validation, and quality control (QC) of in-process material and drug products that is regulated under Subpart F – Production and Process Controls.
Although these regulations are intended to assure that all batches of material share the same characteristics, integrity, and conformity to quality specifications, pharmaceutical manufacturers frequently experience difficulty complying with them. It is critical to recognize and resolve these challenges, as the quality of the manufacturing process ultimately affects patient health and regulatory compliance.
Sampling and Testing: Maintaining Consistency and Validity
One aspect of compliance is ensuring that in-process materials and drug products are accurately sampled and tested. Written procedures are important to specify in-process controls and tests and examinations performed on each batch before release. Yet, quite a few manufacturers either have sporadic sampling methods or too small of a sample size and not enough testing protocol in place. Solving these issues necessitates implementing a detailed set of procedures and ensuring their consistent and sustainable application throughout the enterprise’s manufacturing operations.
Statistical Rigor and Consistency in Validation & Specifications:
The development of valid in-process specifications can create another compliance hurdle. These specs need to conform with final product specs and be based on valid process averages and variabilities. Nevertheless, manufacturers may struggle in their pursuit of utilizing appropriate statistical methods to produce accurate estimates relating to process variation. This can be resolved by using statistical experts or consultants who should be able to guide you on what would needs to be done statistic wise and whether regulation decision criteria has been fulfilled.
Lack of Oversight and Expert Compliance may lead to Quality Control Unit Errors:
QC unit plays an important role in approval or rejection of in-process materials, as well as performs the required tests that are essential in different phases of production. QC errors can stem from ineffective training or other scenarios where the quality control unit does not have sufficient personnel to ensure that non-conforming materials are identifiable, or by mistaken approval of out-of-specification materials. With strong training programs and a culture of quality and accountability, manufacturers can bolster their quality systems and compliance efforts.
Quarantine and Disposal of Rejected Materials:
Avoiding Accidental Use, effective control over in-process materials is another challenge when it comes to compliance. A good quarantine system should be implemented because using the wrong materials in later manufacturing or processing activities can lead to dire consequences. Lessons learnt from the recalls include failure to de-couple and/or provide proper documentation of rejected materials or not labeling them properly which can lead to use of expired material with quality and security problems for the ultimate drug product. These compliance risks can be attenuated by the implementation of more holistic tracking systems, better labeling and improved communication protocols.
The Way Forward: Dealing with Compliance Conundrums Together
To overcome these challenges related to compliance, pharmaceutical manufacturers must abide by the culture of compliance. This includes the ongoing training of employees in manufacturing, quality, and regulatory functions. Compliance with the Current Good Manufacturing Practice for Finished Pharmaceuticals is additionally improved when regulatory experts are actively engaged and their solutions leveraged through state-of-the-art technology.
Conclusion
Current Good Manufacturing Practice in Finished Pharmaceuticals establishes important rules designed to protect the quality and safety of finished pharmaceutical items. However, a few areas prone to compliance challenges include sampling and testing (and associated risk analyses); validation and specifications; quality control unit functions; and the handling of rejected materials. These challenges can be effectively tackled using a combination of robust procedures, training and consulting services; together this enables pharmaceutical manufacturers to maintain the highest level of compliance for their products and ultimately support public health.
Reach out to BioBoston Consulting or visit our website to learn how we can help your organization.
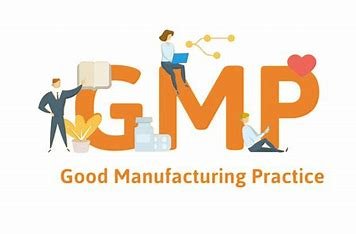