“Learn how integrating servicing with complaint handling and reporting improves medical device safety, compliance, and post-market surveillance.”
With the progression of technology and with medical devices being more complex and interconnected than ever, there is no doubt that servicing them well will be essential. Continuous and effective functioning of medical devices is necessary for the safety of patients, but it is equally necessary to preserve the reputation and standing of manufacturers within the healthcare market. Accordingly, the QSR requires manufacturers to develop and maintain detailed instructions and procedures for servicing their devices and that these instructions meet certain stipulated requirements.
What is Servicing in medical devices?
Servicing, per the QSR, is maintaining (e.g., calibration, inspection), repairing or modifying a medical device to meet specified requirements throughout the life of the device. This is an essential part of the medical device life cycle, implemented to protect patient safety and ensure medical device effectiveness. It is the responsibility of manufacturers to create and keep instructions and processes used for servicing their machines, which must meet specified requirements.
Servicing plays a critical role in quality management
Preventing Device Malfunctions: As medical devices undergo wear and tear over time, regular servicing helps ensure that they function as intended throughout their operational lifecycle. Considering that medical devices are frequently complex with delicate components, and precise engineering, With time these devices can be damaged, or their performance can degrade due to use, environmental factors, or other reasons. By regular maintenance, manufacturers could detect problems long before they become a problem and extend the life and performance of the device. Servicing ensures that the devices are in good condition, thus improving patient outcomes while minimizing possible adverse events being recorded.
Adherence To Regulatory Requirements:
Healthcare compliance on regulations is high on the priority list of any medical device industry. The Food and Drug Administration (FDA) has created a complex guideline to guarantee that all medical devices are safe and effective. Compliance with the servicing obligations in QSR shows how manufacturers ensure that their design, manufacture, and performance meet only the highest quality standards. Adhering to these rules not just helps in abiding by the guidelines but also improves trust from healthcare providers, patients, and regulatory authorities.
Risk Mitigation:
Servicing is a way to pick up and mitigate potential risks related to medical devices. Manufacturers can identify trends or persistent issues via ongoing assessment of service reports analyzed with proper statistics, as required by the QSR. This approach enables them to proactively act on other actions for adverse events and safety of the devices. This method enables reliable detection and mitigation of any risks or problems ontime, thus preventing device malfunctions from taking place and further protecting the patients.
Post-Market Surveillance:
Test and inspection data from servicing are invaluable in post-market surveillance. Post-market surveillance is the monitoring of medical devices after they are commercially released to a monarch market. By enabling manufacturers to analyse service reports when they are received through the systematic collection of data, it allows them to understand how well their devices are performing, identify case studies or patterns of failure and provide remediation in a timely manner where required. This real-time monitoring allows manufacturers to quickly address any safety issues that come up and take action where devices may need improvement in regard to performance and safe usability.
Adding Cost of Complaint Handling & Reporting to Servicing
Manufacturers are required to handle service reports like complaints under the QSR. A service report, however, might address an event that needs to be reported under part 803 of Title 21 and the service report is thus automatically deemed a complaint. Therefore, it also needs to be managed in accordance with the requirements of § 820.198–Complaint Handling and Reporting.
Complaint Handling
It is an integral part of Medical Device Quality management systems. When a specific complaint or service report comes in, the manufacturer must follow a particular procedure of how they would investigate, determine cause, and take corrective and preventive action wherever required. Integrating complaint and reporting processes with servicing ensures that post-market surveillance is performed holistically for better patient safety and compliance by manufactures.
Key Data in Service Reports
Service reports should provide necessary details for traceability, analysis, and compliance. This information includes:
Description of Device Serviced: Accurate identification of the device under service is essential for maintaining proper records and traceability.
Any unique device identifier (UDI) or universal product code (UPC): UDIs and UPCs are ID codes that consist of numbers and text that distinguish a medical device from others in the marketplace. So, by adding them in the service reports, we can accurately follow up on each device individually at various points throughout their lifecycle.
Additional Device Identifying Information(s) and Control Number(s) Utilised: Medical devices may, in some respect be designated a variety of identification or control numbers. These further identifiers assist in ensuring that the records are accurate and expedites tracking.
Date of Service: Maintaining the timestamp for when servicing takes place is important to tracking device maintenance history and timely servicing.
Well-known Person Responsible for Servicing the Device: Entering the name or identifier of a person involved in servicing provides accountability and traceability of actions taken.
Comprehensive Description of the Service Performed: This does not only come in handy from a record-keeping perspective, but it forms an important part of understanding what was changed and/or within the scope of the service performed.
Test and Inspection Data for the Serviced Device: Test and inspection data reports are important for understanding how different the device was before and after servicing. This data helps evaluate how well servicing is going and servicing deficiencies.
Servicing is a fundamental aspect of the medical device commitment to patient safety and product quality. Manufacturers endeavor to assure that their devices fulfills specified requirements and produces the desired results by establishing well-defined servicing instructions and procedures during the manufacture of the device, a process known as Servicing. In addition, combining servicing with complaint handling and reporting systems enables a more holistic approach to post-market surveillance and corrective actions when appropriate.
Conclusion
By embracing servicing as a key component of quality, medical devices can build trust and confidence in healthcare workers and ultimately patients. By focusing on quality through responsible servicing, manufacturers are ensuring that the healthcare landscape becomes safer and reliable, well within accepted levels of quality and patient care.
Get in touch with BioBoston Consulting today or check out our website to see how we can help your organization.
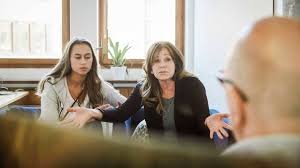