Learn about Sec. 211.208 regulations for drug product salvaging, including best practices, lab tests, inspections, and expert guidance to ensure quality, safety, and public health after improper storage conditions.
Introduction:
The pharmaceutical industry is the frontline for public health by making various medications to treat numerous medical conditions and improve millions of peoples’ lives worldwide. Regulatory bodies such as the Food and Drug Administration (FDA) abide by stringent regulations to ensure these meaningful medications are safe and effective, including Sec. 211.208 Under Subpart K — Drug Products that were Returned and Salvaged. This landmark regulation provides guidance for the salvaging of drug products that have experienced conditions of improper storage due to natural disasters, accidents, or other equipment failures. In pursuit of patient welfare, following Sec., 211.208,best-practices for drug product salvaging are critical new tasks for the pharmaceutical industry.
How Drug Product Salvaging Affect Public Health
Drug product integrity maintenance is key to public health, particularly. Both drug manufacturers and distributors have the onerous task of ensuring that medications retain their effectiveness, quality, and safety until they reach the patient. But external factors can sometimes ignore these key elements, and this creates a major problem for patients as well as the entire pharmaceutical industry.
Drug storage under uncontrolled or inappropriate condition (such as extreme temperature, humidity, smoke, fumes, pressure, age or radiation) can dramatically affect the chemical composition and therapeutic properties of this drug. In addition, natural disaster (hurricane, earthquake, fire), as well as unanticipated accident (equipment failure) can make storage of drug product more difficult and pose a threat to public health. It is in such environment, Sec. 211.208 regulation applies as a useful guide for assessing the appropriateness and feasibility of salvaging a drug product under an established stringency of quality standards.
Given that drug products are important in providing patient care, adherence to Sec.211.208 is non-negotiable for pharmaceutical manufacturers, distributors, and regulatory authorities. With the understanding of the criteria set by the regulation and following these best practices, companies can go ahead with salvaging.
Understanding Sec. 211.208 Salvaging Drug Products
Sec. Section 211.208 protects the public health by ensuring that adulterated drug products are not reintroduced into commerce. Pharmaceuticals have an effective use-by date; however, improper storage conditions involving temperature (frozen or overheated), humidity, smoke/fumes, pressure, age and/or radiation can play a major role into the workings of pharmaceuticals making them ineffective or downright harmful to the people. When dealing with such instances, salvage operations performed should be a matter of utmost regulation compliance.
Criteria for Salvaging Drug Product
Show laboratory tests and assays Results:
Laboratory tests and assays are critical to deciding if the drug products were sufficiently produced within specification. They include an assurance of the identity, strength, quality and purity of the drug. Examining the chemical composition and stability of retrieved drug products requires the use of sophisticated analytical methods, including high-performance liquid chromatography (HPLC), gas chromatography, mass spectrometry (GC-MS) and spectroscopy.
In addition, simply due to the lack of human-based safety and efficacy studies for some medications, animal feeding studies may also be needed. Such rigorous checks are necessary to ensure that the recovered drugs are still fit for human use. These studies yield critical pharmacokinetic, toxicology and efficacy data in a blinded setting on living animals of the species used for clinical trials on end-users, thus guiding whether or how a drug product may be salvaged.
Inspection of Packaging & premises:
In addition to lab testing, a visual inspection of the premises is also important to confirm if inappropriate storage conditions resulted from natural disasters, accidents and/or equipment failures. This inspection should be aimed at the storage area, temperature control mechanisms, and packaging integrity. When the packaging of a drug product is damaged, deteriorated or corroded, it can open a door to contamination causing potential adverse effects on product quality. This is why it becomes essential to keep the protective characteristics of packaging materials intact even when exposed to extreme temperature at which they are stored.
Teams should involve expertise like QC engineer, Tar opener to see how much damage caused by disaster or accident. Information obtained on inspection will provide the basis for assessment of salvaging drug product.
Additional Evidence: Sensory Evaluations
Although lab-reports and inspections serve as the main evidence to support the salvage of a drug product, organoleptic examinations may also offer complementary evidence. Organoleptic examinations provide information on drug products based on assessment through senses (e.g., taste, appearance, aroma, and texture).
Trained personnel and experienced staff may evaluate by their senses any signs of degradation, contamination or off-odors in the drug products. However, these tests should not be used alone as conclusive evidence and instead they can only be used as complementary information. The organoleptic evaluations further complement the analytical findings to provide a more integrated perspective of overall drug product quality.
Salvaging Drug Product: Best Practices
To correspond with Sec. 211.208 and to protect public health, pharmaceutical manufacturers and distributors should adhere to the following best practices when salvaging drug products:
Robust Documentation:
Record keeping, including documenting drug product name and lot number, along with its disposition. Meticulous records are essential to monitor salvaged medications and determine the transparency of the process. During FDA Inspections and Internal Audits, these records should be available to demonstrate compliance with regulations.
Immediate Action:
Any time where there is the possibility that drug products may be compromised, act quickly to quarantine any affected batches from reaching the marketplace. Appropriate assessment and mitigation are critical to reducing the potential consequences of harmful storage conditions, so that these adverse circumstances do not affect drug product quality.
Expert Assessment:
Conduct laboratory tests and assays, and make inspections with qualified professionals. Their expertise helps to make reliable assessments of drug product viability. Partnering with trusted third-party labs and unbiased experts can also add an objectivity that accompanies the salvage process.
Compliance with cGMP:
Follow the recently established good manufacturing practices (cGMP) guidelines during the salvaging so that optimum quality standards can be fulfilled. These are all aspects to be calculated to the very exact, belong under the umbrella of GMP (good manufacturing practices) — this includes facility layout, equipment calibration, process validation and personnel training.
Risk Mitigation:
Conduct risk assessments to detect risks and hazards of drug product salvaging. Plans for risk management should be formulated, implemented and should ensure that risks to the quality and safety of the product are adequately controlled.
Careful implementation of regulations — Sec. 211.208 demonstrates the drug industry’s loyalty to protecting public health by Salvaging of drug products. The global phenomena of natural disasters, accidents or equipment failures leads drugs to harsh conditions for storage – the topic demands a holistic approach, merging science based on human experience and ethical considerations.
Given the critical nature of safety risks posed by reclaimed drug products, laboratory tests and assays can be crucial to rehabilitation efforts. No question about it—those evaluation findings ensure that any recovered medications adhere to carefully controlled standards of identity, strength, quality and purity. Along with lab assessments, onsite packaging inspections are important evidence to verify if the claim about inappropriate storage conditions is substantiated. All inspections are done by experienced professionals with diversified skillset, and attention is paid to even fine details to avoid compromising salvaged drug products.
Organoleptic examinations
It bolster analytical results with the human component of sensory practices (especially given today’s increased interest in quality control and patient safety). However, they are still supplemental and solid scientific evidence should be at the forefront of decision-making.
The pharmaceutical industry is committed to maintaining the highest standards of cGMP during the drug product salvaging process, and this can be achieved by incorporating best practices. Timely and decisive actions to mitigate risk combined with thorough recordkeeping to provide transparency to regulators or consumers if needed represent cornerstones of salvaging excellence.
Conclusion
The Regulation is one of the fundamental building blocks of drug product safety, integrity and efficacy. Adopting this regulation and saving drug products using best practices is a reflection of pharmaceutical industries worldwide commitment to public health and the patients. By implementing strict quality standards, working with experts, and remaining incredibly vigilant, the industry preserves salvaged drug product to keep playing their role in reducing pain and improving lives.
To find out more about how we can assist your organisation, contact BioBoston Consulting or browse our website.
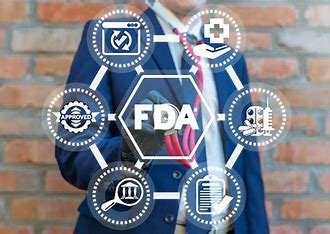