“Ensure compliance with FDA’s Current Good Manufacturing Practice (cGMP) regulations for laboratory controls. Learn about specifications, sampling plans, in-process material testing, and quality assurance in pharmaceutical manufacturing.”
The cGMP regulations highlight the necessity of both establishing and documenting control mechanisms. It also involves preparing specifications, standards, sampling plans, test procedures and other quality control measures. These activities require the participation of the relevant business unit to ensure that you have correct and complete controls. Combining knowledge from relevant areas of manufacturing, quality control, regulatory affairs, and others, pharma companies will create strong lab control hurdles to meet the expectations in Subpart I.
Pharmaceutical production should be performed according to strict regulation to ensure the security of drug safety, quality and efficacy. Regulations that play a key role are Title 21, Chapter I, Subchapter C, Part 211 — the Current Good Manufacturing Practice (cGMP) for Finished Pharmaceuticals. Guidance issued by FDA, an agency of the Department of Health and Human Services (HHS), governs laboratory control systems for drug manufacturing.
General Requirements
Under these cGMP regulations, there is the requirement to include documentation of various laboratory control mechanisms. Following are some tips to help you assure compliance with the general requirements of Subpart I:
Involvement by Each Organizational Unit:
The organizational unit (i.e., manufacturing, quality control, regulatory affairs) should appropriately be involved in the development of specifications, standards, sampling plans, test procedures and other laboratory control mechanisms as it pertains to each organizational unit. Including relevant stakeholders allows you to tap into their knowledge and ensure that such controls are thorough and accurate.
Documentation
Documentation is an important part of the compliance of cGMP regulations. The date of compliance must be documented as part of performance records required by Subpart I. Retain complete specifications, standards, sampling plans, test procedures and deviations from these controls with justification. Documentation should be easily accessible, organized, and reviewed periodically for improved compliance management.
Laboratory Controls
Laboratory controls are essential to ensure the identity, strength, quality, and purity of components (including containers), drug product containing closures, in-process materials, container closure systems, labeling and drug products. a) Specifications and Sampling: Establish scientifically sound and suitable specifications, sampling plans, and test methods for all components, drug product container/closure system in-process material labeling, and drug product. These specifications can be drawn from established science which would assure products are up to standards. Also provide descriptions of sampling and testing in the specs designed so that staff involved in production line can easily comprehend it.
Sampling: As applicable, obtain representative samples of each lot from each shipment of components, drug product containers, closures, and labeling. These must be accurately labelled to ensure traceability. Sampling procedures should consider the nature of materials and related risks.
In-Process Material Testing:
In-process materials are essential intermediates involved in the process of pharmaceutical manufacturing. Define written specifications and in-process sampling procedures for in-process materials (e.g., ingredients, packaging material) used to produce a dietary ingredient to ensure they meet appropriate standards of quality. These specifications are expected to be consistent with the planned use of the materials and the characteristics required of the finished drug product. Obtain representative samples of in-process materials as with other testing procedures, properly identified for testing purposes.
Drug Product Testing:
Written description of sampling procedures and applicable specification are needed for drug product. SOPs specifying how the samples are to be taken and what tests will be performed on them to check their quality/requisite measurement are necessary. The representative samples should accurately reflect the attributes of the entire group of drug products. This traceability between the samples is maintained throughout the production cycle by appropriate identification of each sample.
In-house calibration of instruments / Apparatus / Gauges and recording devices
There should be a documented procedure, ensuring that steps, schedules, accuracy and precision limits are defined along and with the means needed to take corrective action if the accuracy and/or precision is not met. Calibrate and qualify instruments according to established specifications. Instruments that fail to adhere to calibration specifications should be taken out of use until recalibrated or repaired to restore accuracy and reliability.
The Current Good Manufacturing Practice for Finished Pharmaceuticals by the American Food and Drug Administration is an important regulation in the pharmaceutical industry as it governs everyday practices of manufacturers that affect product safety and quality. Compliance with the provisions defined under Subpart I of Part 211 allows for strict laboratory controls and consistency in manufacturing procedures.
Conclusion
This comprehensive set of tips and advisories leads the social responsibility in navigating the regulatory landscape by ensuring compliance with the cGMP regulations. Compliance is a continuous process, and periodic reviews and updates on laboratory controls are necessary to remain compliant with the changing regulatory landscape. Pharmaceutical manufacturers can enhance their reputation, safeguard consumer health, and promote the growth of the pharmaceutical domain with stricter compliance regulations and laboratory control processes.
To find out how we help your organization, reach BioBoston Consulting or visit us now.
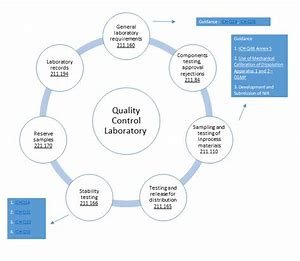