Explore the critical importance of process validation in the medical device sector, including its role in enhancing safety, ensuring regulatory compliance, and fostering continuous improvement.
Adherence to quality standards is crucial in the medical device industry because of its prolific nature. Part 820 — Quality System Regulation, Subpart G of the FDA’s guidelines (21 CFR 820.75) dealing with “Process Validation” is one that cannot be overlooked.
Process Validation- The Heart of the Process: It provides an assurance all processes for medical device are consistently meeting quality and its attributes for intended use. Process validation ensures that each medical device manufactured is safe, effective and reliable.
Process Validation Breakdown- Key Components of Process Validation
Written Validation Procedures: It is important for all validation procedures to be documented thoroughly sor that the manufacturer can confirm if the process meets the assigned specifications.
Capable Personnel: Staff, who are able and have been trained on validated procedures are essential to maintaining product quality and safety at the highest levels, which in turn reduces risk of deviations.
Establishing procedures for continuous monitoring and control of process parameters further guarantee a stable compliance to specifications, enabling early detection and correction of any variation.
Review and Evaluate Deviations: Timely and complete deviation reviews of deviations in the manufacturing process followed by revalidation preparation assures a good quality product, ultimately avoiding further risks.
Product quality control creates a bubble over the manufacturing or deployment process and micromanages how production chain is executed until product validation is confirmed. The procedure helps stabilize every critical aspect of your medical device and fulfill customer satisfaction by delivering high-quality devices for patients. .
Improved patient safety: Process validation confirms that the devices are less prone to error thereby ensuring patient health and safety by avoiding risks of bad medical device r
Regulatory Compliance – Strict adherence to the regulations such as process validation is key for FDA approval and an essential method of showing good product quality avoiding recall and protecting brand equity.
Cost Savings: Prior detection and correction of issues in the production cycle reduces expensive errors, saving on resources, enhancing production efficiency which means better cost control, offering competitive market prices.
Continuous Improvement: The process validation promotes continuous improvement. Manufacturers are able to combine new technologies helping them embrace newer methodologies and grant their organizations a culture of innovation as well as safe operations.
Conclusion
This dedication to strong process validation is a badge of honor for conscientious medical device manufacturers. When they put process validation at the top of their list, companies can protect patients and enable medical technology to evolve.
Reach out to BioBoston Consulting today or check our website to find out how we can help your organization.
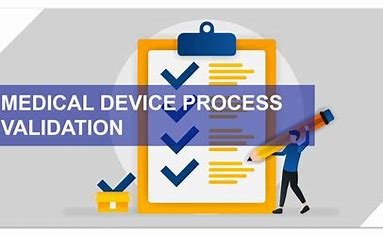